19 Jul
Waste not want not: creating value from our wastewater
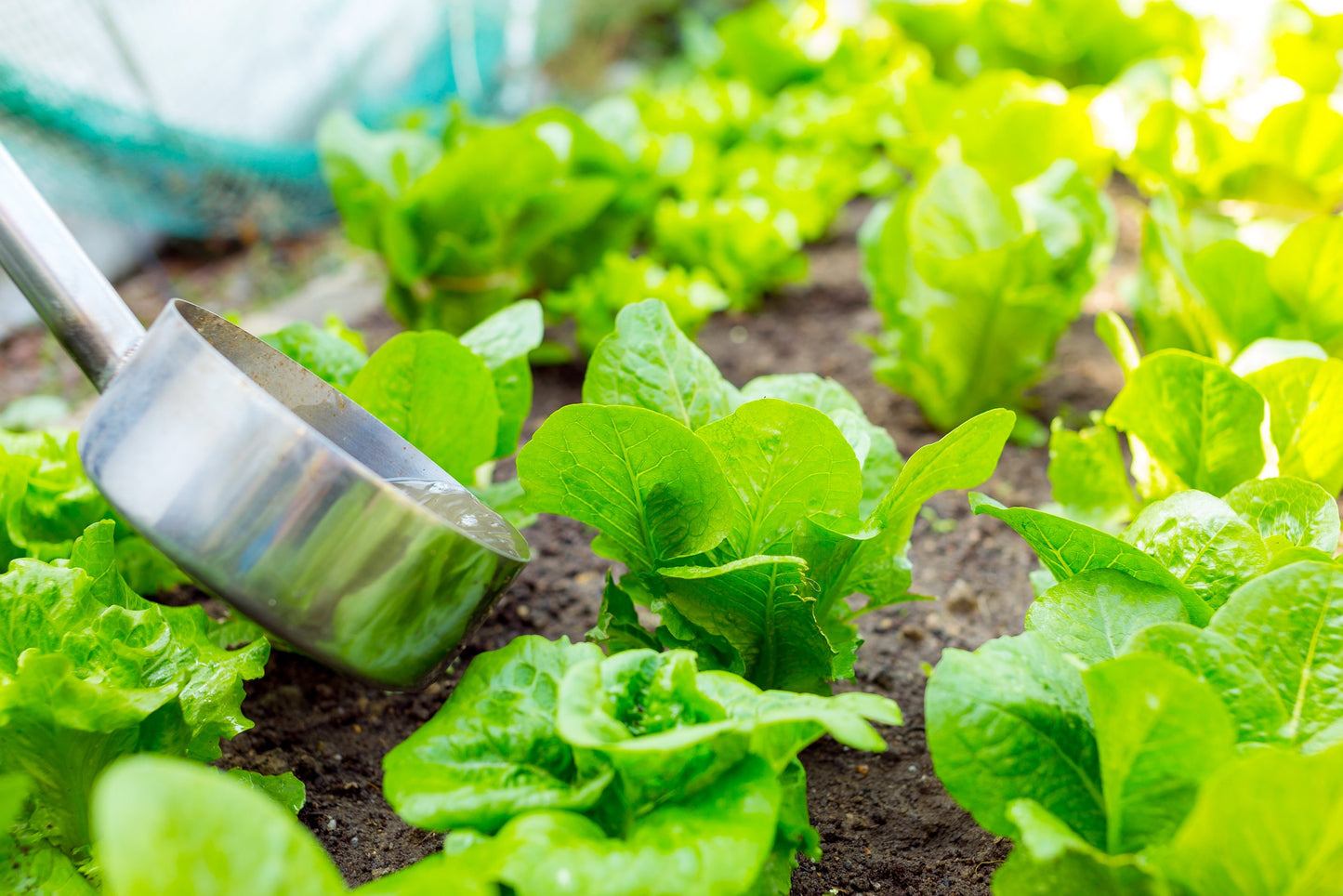
The ultimate goal in sustainable manufacturing of any kind is “circularity”, meaning any waste in a process becomes something useful, and that only potentially useful things become waste in the first place. But in most of the human economy, including food and drink manufacturing, “linear” production methods are the norm. Essentially, we extract raw materials, make a thing, then throw away the waste. And no matter how far removed from nature we think we are, the human economy exists under the same constraints as the natural world. In nature, there is no such thing as “away”. To paraphrase Mufasa’s speech in The Lion King, everything is connected through cyclical processes and there is no such thing as waste in nature. One living thing’s waste is another living thing’s food in the great circle of life.
To make our Dutch Barn Orchard Vodka, we take British apple juice, ferment it into cider, take the alcohol from the cider and then send the alcohol-free and nearly sugarless stewed apple juice for treatment before its ultimate disposal. This is a perfectly safe way of doing things, but it’s still a linear process. We’ve done some analysis on this waste stream and know that it has lots of valuable components for plant growth: nitrogen, phosphorus, and potassium (the main components in commercial fertilisers) as well as micronutrients such as boron, copper, and zinc.
Working in partnership with the University of York’s Biorenewables Development Centre, with funding from Innovate UK, we’ve started a project to extract these components for their use as a natural, slow-release fertiliser known as struvite. Struvite is a mineralised form of fertiliser that slowly dissolves near plant roots, where there is increased acidity in the soil. Because the nutrients contained within struvite release slowly, there’s great potential to decrease instances of nutrient run-off into watercourses.
Not only could this project result in a linear process turned circular, but it also has the potential to reduce greenhouse gas emissions. The main production methods for commercial fertiliser products rely on non-renewable resources. In the case of nitrogen production, fossil gas is first used create ammonia before synthesising different nitrogen fertiliser products. Phosphorous and potassium fertiliser products are mined, which again is a linear, non-renewable process. It’s no surprise then, that as the cost of energy increases, the cost of fertilisers also increase. According to figures from the UK’s Agriculture and Horticulture Development Board, the price of UK-produced ammonia nitrate fertiliser in Great Britain increased by 152% since between May 2021 and May 2022. Prices of the same imported fertilisers increased by 171% over the same period. The price of potassium chloride fertiliser (potash) has increased by 165% and phosphate fertilisers has increased by 120-128%. While the UK currently produces 40% of its fertiliser requirements, one of the UK's two major fertiliser plants has permanently closed, raising concerns about competition in the UK fertiliser industry.
With this project, we’re trying to determine the methods and costs required to extract fertiliser nutrients from our waste, as well as the efficacy of the extracted nutrients and leftover water for use in commercial agricultural systems. If the project is successful it would allow us to close the loop on a business process which is currently linear, and might even create a new revenue stream for our business. Early results show that we can, in fact, extract fertiliser compounds from our waste stream. We’ll also conduct plant growth trials with the remaining, struvite-extracted, liquid to determine whether the liquid part of our waste could be applied to crops as irrigation. The first stage of this project is due to finish in April 2023, so watch this space for more updates!